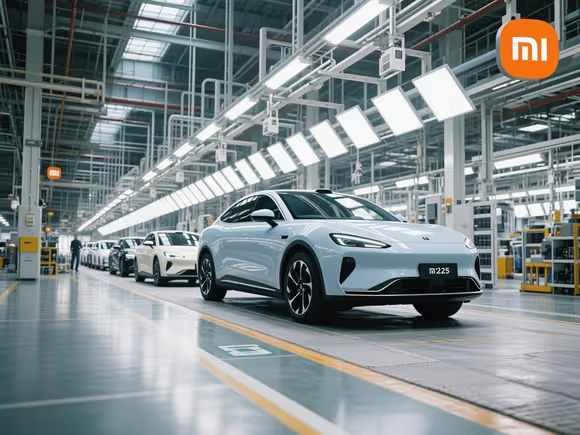
截至 2025 年,小米汽车生产车间已形成以北京为核心、辐射全国的智能制造体系,其技术创新与产能布局展现出显著的行业竞争力。以下是基于最新信息的深度解析:
一、产能布局:南北双基地协同发力
- 北京亦庄超级工厂
- 一期工厂:设计年产能 15 万辆,通过生产流程优化,2024 年实际产量已突破 13.5 万辆。2025 年采用双班生产模式,每小时产能提升至 40 辆,关键工艺 100% 自动化。
- 二期工厂:位于通州马驹桥,2025 年 4 月完成规划验收,6 月启动试产,8 月正式投产,新增产能 15 万辆 / 年,总产能突破 30 万辆。工厂采用 “可变形工厂” 设计,兼容多车型共线生产,单线改造成本仅 2 亿元,支持新车研发周期缩短至 11 个月。
- 武汉生产基地
- 规划占地 2000 亩,定位华中市场,预计 2025 年启动建设,2026 年投产,初期产能 30 万辆 / 年。工厂紧邻小鹏、路特斯生产基地,形成产业集群效应,缩短交付半径。
二、生产技术:智能化与轻量化双轮驱动
- 超级工厂核心技术
- 9100 吨压铸岛集群:规模超过特斯拉上海工厂,通过 72 合 1 一体化压铸技术,将后地板零部件数量从 72 个减少至 1 个,焊点数量降低 90%,维修成本下降 50%。
- CTB 电池技术:电池与底盘一体化集成,提升车身扭转刚度 20%,续航里程增加 12%,SU7 Ultra 搭载宁德时代第二代麒麟电池,15 分钟补能 510km。
- 智能质检系统:采用 X 光 AI 检测(28 次 / 压铸件)、激光雷达在线检测(精度 0.05mm)、紫外光外观检测(精度 0.05mm),缺陷识别准确率达 99.9%。
- 轻量化革命
- 蜂窝铝镁合金型材:通过投资定制化型材企业,将车身减重 15%,成本从 380 元 /kg 降至 120 元 /kg,SU7 Ultra 白车身重量降至 320kg,较 Model Y 轻 18%。
- 材料替代策略:前双叉臂悬架替换为麦弗逊结构,单辆车节省 2000 元;铝制副车架减重 30%,抗冲击性提升。
三、车型与产能分配
- 主力车型
- SU7 系列:2025 年 3 月交付量突破 2.9 万辆,全年目标 35 万辆,其中 Ultra 版本占比 25%-30%,搭载三电机四驱系统,零百加速 1.97 秒,售价 52.99 万元起。
- YU7:首款 SUV 车型,定位 30-40 万元市场,6 月上市,由二期工厂生产,规划年产能 15 万辆,搭载激光雷达与高阶智驾系统。
- 产能分配
- 北京一期工厂主攻 SU7 标准版,二期工厂聚焦 SU7 Ultra 与 YU7;武汉基地未来承接入门级车型 “昆仑”(增程式 SUV,售价 15 万元起)。
四、供应链与成本控制
- 核心供应商
- 电池:宁德时代(麒麟电池)、比亚迪(刀片电池),通过战略投资确保优先供应。
- 轻量化材料:祥鑫科技(电池包结构件)、拓普集团(空气弹簧)、芯联动力(碳化硅电控模块)。
- 智能驾驶:Mobileye(EyeQ5 芯片)、地平线(征程 6 芯片),自研 BEV 大模型实现端到端智驾。
- 成本优化
- 垂直整合:自研压铸机、碳化硅电控模块,摊薄研发成本;投资型材企业,实现车规级蜂窝铝镁合金量产。
- 生态开放:允许友商采购小米供应链产品,如定制型材,进一步降低边际成本。
五、环保与可持续发展
- 绿色制造
- 光伏电站:北京工厂屋顶光伏装机容量 16.2MW,年发电量 1640 万度,减排二氧化碳 1.3 万吨。
- 废水处理:涂装车间废水循环利用率 80%,重金属零排放;电泳槽清洗水超滤回收,减少新水用量 80%。
- 材料循环:碳纤维车身部件回收率达 95%,电池梯次利用技术应用于储能领域。
- 低碳供应链
- 与宁德时代合作开发 “零碳电池”,2025 年实现 10% 产能绿电生产;铝镁合金型材生产采用可再生能源占比超 60%。
六、未来挑战与展望
- 产能爬坡压力:2025 年 35 万辆交付目标需二期工厂满产,且武汉基地按时投产,供应链稳定性(如芯片、电池)是关键。
- 技术迭代风险:特斯拉 “纳米晶格钢”(密度比铝低 50%)计划 2026 年量产,可能冲击小米轻量化优势。
- 全球化布局:SU7 Ultra 已进入欧洲市场,未来需在东南亚、中东等地建立本地化生产基地,规避贸易壁垒。
小米汽车通过 “自研 + 投资” 模式,构建了覆盖生产、供应链、环保的全链路竞争力,其 2025 年生产车间的技术突破与产能释放,将加速中国智能电动汽车产业的升级进程。
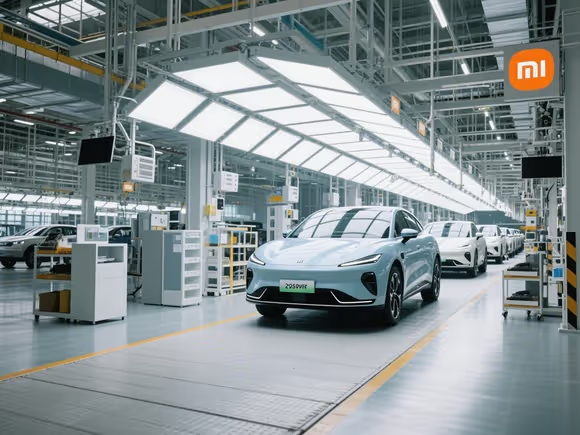